A tree with European ties and an American heritage
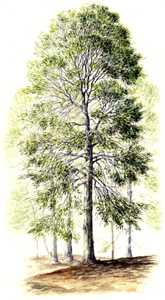
Long ago, English bodgers crafted the legs of Windsor chairs from beech trees they felled in the forest. The long- wearing wood also became peasant footwear in the shape of shoes and clogs. And in the iron smelters of Germany, France, and England, beech was the fuel.
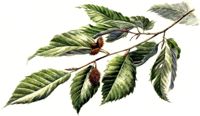
The vast beech forests that once covered large parts of Indiana, Kentucky, Ohio, and central Michigan were thus familiar to early European immigrants and travelers. But westward-moving pioneers in the new land dicovered that the American beech grew in the choicest soils. So with ax and saw, they felled the trees to plant crops. In doing so, they destroyed the nut crop of the then numberless passenger pigeon. This move, combined with mass hunting, spelled their extinction.
Today, although the blanketing beech forests are gone, the tree remains plentiful throughout its range. Its hard, pliable, strong, and pretty wood, however, primarily furnishes stock for paper. That’s because kiln-drying beech in commercial quantities has its pitfalls. Yet, some beech does become woodenware and furniture parts, as well as barrels for aging beer.
Wood identification
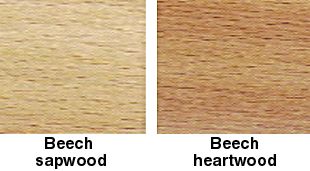
While beech species grow in every hemisphere, the one you’ll find in North America is American Beech (Fagus grandifolia). “Blue beech,” which shares the same range, proves to be hornbeam.
In lower elevations, beech often grows in pure stands, with trees to 120′ in height and 4′ in diameter.
Beech has an unmistakable bark of shiny, silver-grey that fits its trunk like smooth skin. It seems to beg knife-point initialing, as was done by Daniel Boone on a Tennessee tree: “D. Boone, Cilled A Bar On Tree In Year 1760.”
In early spring, yellow-green blooms appear with the newly formed leaves on beech’s branches. By fall, small triangular nuts covered by prickly burs occur. These sweet, edible nuts provide wildlife with forage.
The wood of beech resembles yellow birch, but with a tint of red in the darker brown heartwood. The straight-grained, evenly textured stock frequently has an attractive ray fleck. It is hard, strong, and heavy—at 45 lbs. per cubic foot, it matches red oak.
Uses in woodworking
Because beech steam-bends as readily as ash, it works well for chair legs and backs. In fact, this under-used wood could be made into any type of interior furniture, cabinets, flooring, and trim. As drawers, beech actually becomes slicker as it rubs against other wood members.
Woodturners use beech for items such as goblets with delicate stems. It’s also ideal for food-use vessels like cutting boards and spoons because it imparts no odor or taste, and takes abuse. Carvers, though, find it difficult to tackle.
AvailabiIity
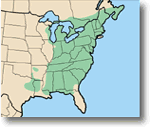
Beech may not fill a bin at your hardwood retailer, especially if you live far from its range. However, the large suppliers that carry this hardwood normally offer it at a price below that of hard maple. And, you may find it in long boards up to 12″ wide, but usually not as plywood.
Slow-grown beech from the northern part of its range will give you the most woodworking satisfaction because of its tighter grain. But avoid stock that’s only air-dried or you’ll invest as much work getting rid of warp, twist, checking, and discoloration as you will making parts. Otherwise, work the wood using the following tips.
Machining methods
Beech reacts to most machining much like maple or yellow birch, with some exceptions:
- Beech’s hardness sometimes means chipping or tearout when planing or jointing with revolving cutterheads. If this happens, try reversing the board and taking a shallower cut.
- Deciding on grain direction when feeding the jointer can be a problem because of the evenness of beech’s grain. If it gets confusing, simply set the table height for a 1/16″ cut and proceed. If there’s no tearout, gradually increase the cut to 1/8″.
- Nearly as dense as hard maple, beech requires ripping with a rip-profile blade of 24 teeth or fewer to prevent dust buildup and burning in the kerf. Don’t try to feed the wood any faster than the blade wants to cut it, and use your saw’s splitter to defeat binding.
- Depend on a fine-toothed cross cut blade to cut beech to length, again to prevent burning.
- When drilling beech, back the bit out frequently to clear the hole. This avoids burning, especially in end grain.
- Ballbearing pilots on your router bits and slow feed will eliminate burning. So will shallow passes across the grain.
- Beech works well with all glues. Detect squeezeout by wiping along the joint with paint thinner.
- Because of beech’s hardness, always predrill for fasteners.
- Unlike maple, beech won’t blotch when stained, and you can stain it to resemble other woods, particularly cherry.
- You’ll find that beech accepts all types of finishes equally well. If you have stock with a distinct ray fleck, enhance it with clear penetrating oil.
Carving comments
Although generally not a carver’s choice for hand tools, beech can be shaped with power carving burs. But don’t start with aggressive burs. Use medium, then fine.
Turning tips
An excellent turning wood, beech presents few problems other than its hardness, which results in scratches if sanding is done across grain on the lathe. Always sand with the grain while the lathe is turned off.
SHOP-TESTED TECHNIQUES THAT ALWAYS WORK
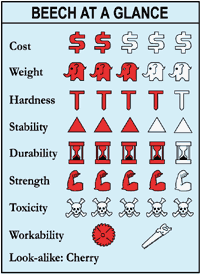
Any exceptions, and special tips pertaining to this issue’s featured wood species, appear elsewhere on this page.
- For stability in use, always work wood with a maximum moisture content of 8 percent, with 6 percent preferrable.
- Feed straight-grained wood into planer knives at a 90° angle. To avoid tearing, feed figured wood or that with twisted grain at a slight angle of 15°, and take shallow cuts of about 1/32″.
- For clean cuts, rip with a rip-profile blade that has 24-32 teeth. For crosscutting, use a blade with about 40 teeth.
- Avoid drilling with twist drills. In wood, they tend to wander off the mark as well as cause breakout. Use a backing board under the workpiece.
- Drill pilot holes for screws.
- Rout with sharp, preferably carbide-tipped, bits and take shallow passes to avoid burning.
- Carving hardwoods generally means shallow gouge bevels—15° to 20°—and shallow cuts.