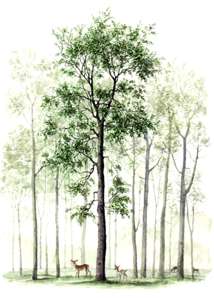
Although today we think of black cherry as one of the classic furniture woods, it wasn’t always that way. Settlers in the Appalachian Mountains, for example, valued the tree’s fruit more than its wood. They dubbed the tree « rum cherry » because from its dark purple cherries they brewed a potent liquor. Also, black cherry’s inner bark contributed to tonics and cough medicines. Elsewhere, though, the wood was more appreciated.
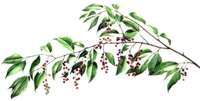
Early New England furniture-makers often found the price of fashionable Honduras mahogany beyond reach and turned instead to native black cherry. Because black cherry wood eventually darkens to a deep reddish brown, these frugal craftsmen mixed what they called « New England mahogany » in with the real thing.
Today, cherry still appears in classic reproductions of colonial style furniture. It has also climbed in popularity as a new look in kitchen cabinets.
Wood identification
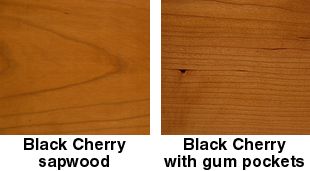
Black cherry (Prunus serotina) ranges from the Missouri River east to the Atlantic Ocean, but the species develops best in the Allegheny and Appalachian Mountains of the East. There, in forest conditions, trees grow to 100′ heights and 4′ diameters.
Young black cherry has satiny, dark, red-brown bark that develops into gray flaky scales as the tree matures. Oval-shaped, pointed leaves appear in the spring. Then, before the new, reddish leaves turn dark green, flowing clusters of white flowers bloom. By late summer, purple, pea-sized cherries appear. Birds eat them and distribute the seeds.
The heartwood of black cherry has a light pinkish-brown color when freshly cut. Sunlight deepens it to a dark orange-red. The cream-colored sapwood, however, never darkens to match.
Black cherry’s straight, close, and finely textured grain generally features a gently waving figure. Sometimes, trees yield boards with rippled or quilted patterns. Dark spots—actually gum pockets—often appear in black cherry heartwood. Avoid selecting these boards, or at least keep pockets to a minimum.
At 35 pounds per cubic foot, black cherry weighs less than maple. And, it is two-thirds as hard but just as strong and stable.
Uses in woodworking
Rated as a fine cabinet and furniture stock by centuries of craftsmen, black cherry has few limits. It takes abuse as tables, desks, and chairs. Black cherry also becomes musical instruments and architectural paneling, as well as millwork. It’s only moderately durable outdoors.
AvailabiIity
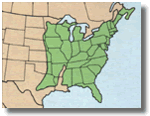
Outlets farther from the source will, of course, charge more. You also can buy black cherry plywood—usually almost twice the price of a sheet of red oak. Turning squares, buttons, and plugs also are available.
Machining methods
Select boards with a minimum of sapwood and gum pockets. Then, remember these tips:
- Black cherry planes extremely well due to its fine, close grain, but take light cuts in jointing. Dull blades burnish it.
- We’ve found that for some reason steel blades burn black cherry less than carbide-tipped blades. Avoid burning by feeding the stock without hesitation. In crosscutting, carbide blades outperform steel.
- Except for the common twist drill, any type of bit does well. However, use slower drill press speeds (about 250 rpm). A pause will burn the wood.
- In routing, black cherry doesn’t chip or tear like maple, but it will burn during a split-second hesitation. Take light passes without stopping.
- All types of woodworking adhesives work well, as long as you carefully control squeeze-out. It mars a clear finish more jarringly than on other woods. To check, wipe joints with thinner.
- Because black cherry is nearly as hard as maple, it scratches easily in cross-grain sanding, so never overlap strokes where joints bring the grain together at right angles, such as the comer of a face frame. For best results, use a cabinet scraper to remove scratches between grit changes.
- You probably won’t want to stain cherry, except to blend sapwood with darker heartwood. For control, we recommend aniline dye. To hasten cherry’s natural tendency to darken, mix a solution of 1or 2 ounces of sodium hydroxide (lye, poisonous) to a gallon of water, brush it on the wood, then neutralize with water. Experiment for shades.
- Although oil finishes and clear lacquers or varnishes work equally well on cherry, you’ll get a smoother finish on this fine-grained wood if you thin the first coat to act as a sealer. Then, sand with 400-grit or 0000 steel wool after it’s dry and recoat.
Carving comments
Although hard, black cherry takes detail and finishes beautifully. For an eye-catching natural-finish carving, follow these suggestions:
- Flat-sawed wood has the most grain pattern; quarter-sawed boards (growth rings perpendicular to the width of the board), the least.
- Power-carving tools fit black cherry. Use carbide burrs.
- To remove small scratches on the finished carving, first sand with a coarse sanding drum followed by a fine sanding drum. Then, go over the piece with a coarse sanding disc, using a rocking motion. Hand-sand with 150-grit, then 320-grit.
Turning tips
Cherry turns nearly effortlessly, as long as you use sharp tools to shear the wood. To sand, shut off the lathe and start with 150-grit, working only with the grain.
SHOP-TESTED TECHNIQUES THAT ALWAYS WORK
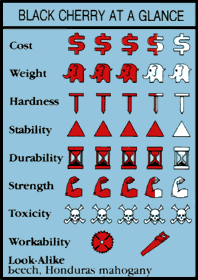
Any exceptions, and special tips pertaining to this issue’s featured wood species, appear under headings elsewhere on this page.
- For stability in use, always work wood with a maximum moisture content of 8 percent.
- Feed straight-grained wood into planer knives at a 90° angle. To avoid tearing, feed wood with figured or twisted grain at a slight angle (about 15°), and take shallow cuts of about 1/32″.
- For clean cuts, rip with a rip-profile blade that has 24-32 teeth. Smooth cross-cutting requires at least a 40-tooth blade.
- Avoid drilling with twist drills. They tend to wander and cause breakout. Use a backing board under the workpiece.
- Drill pilot holes for screws.
- Rout with sharp, preferably carbide-tipped, bits and take shallow passes to avoid burning.
- Carving hardwoods generally means shallow gouge bevels—15° to 20°—and shallow cuts.