From men-of-war to kitchen cabinets, always number one
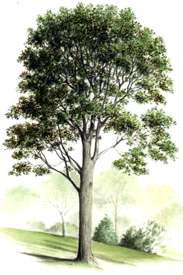
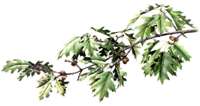
To England’s ancient druids, the oak symbolized strength. Warlike Norsemen even cherished pieces of the wood as charms to protect them from evil. But to the Greeks, Romans, and later seafaring nations, oak meant sturdy men-of-war and reliable merchant ships. In fact, England and France reserved whole forests for use in building their fleets. That’s why red oak from North America saw immediate popularity when it was introduced to those countries in the early 18th century. Within a few years, northern red oak substituted for native English and European oak species and was crafted into furniture and paneling.
Even after centuries of popularity, northern red oak still outsells all other hardwoods. And luckily, it’s plentiful, comprising about one fifth of the standing timber species grouped as red oak.
Wood identification
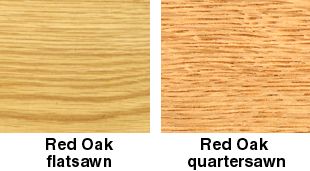
The broad, spreading crown of the northern red oak (Quercus rubra) shades the landscape in a sweeping range that covers nearly half the U.S. and much of southeastern Canada, as shown on the map. More commonly called red oak, but also known as eastern red oak, gray oak, and Canadian red oak, the tree can grow to 150’heights with trunks 6′ in diameter in fertile upland forest soil. Open grown trees more often approach only 70′, with trunks that separate into several large branches.
Northern red oak has distinctive leaves up to 9″ long, with a pointed bristle on each lobe tip. In the spring, flowing catkins of pollen-bearing flowers emerge amid the greenery. Acorns about 1″ long develop every two years.
Rare is the board of northern red oak that carries a trace of its light-colored sapwood. Instead, the vast majority of northern red oak treats woodworkers to nicely figured heartwood with a pinkish tint.
You’ll find that northern red oak has coarse-textured, straight, open grain. This hard, stiff, strong wood weighs 44 pounds per cubic foot dry—just a little more than walnut.
Uses in woodworking
Ever since the early 1970s, northern red oak has been highly favored for kitchen cabinets, and still leads in appeal for all kinds of furniture as well as millwork and flooring. Turners and carvers, too, find the wood a choice stock for decorative projects.
AvailabiIity
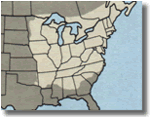
Hardwood dealers and home centers offer northern red oak as lumber, veneer, plywood, turning squares, and dowels. But, all northern red oak won’t be the same. Trees from the North—from the Appalachians on into Canada—grow slower and therefore have a more uniform color and a finer, easier-working texture than those from the South. Other characteristics remain the same, though. And, no matter where the wood hails from.
Machining methods
As most woodworkers will attest, red oak works wonderfully, but it does require power tools. Even then, the wood sometimes takes special handling. Our observations:
- Feed red oak on the jointer so that the knives’ rotation follows the direction of the grain flow (see sketch, below). Failure to do this generally produces chipping.
- Due to red oak’s open, straight grain, it offers only moderate resistance to ripping.
- Red oak quickly dulls anything other than a carbide blade.
- Too fast a feed rate on the table or radial-arm saw, or with the router, can cause burning, although burns sand off easily.
- Red oak tends to splinter. So, use shallow router passes on end grain and a backing board clamped to the exit side on cross-grain work.
- Metal, such as a clamp bar, touching glue squeeze-out produces a dark blue stain. Lay wax paper over the glue line.
- Red oak grips screws, but even with pilot holes, lubricating the threads with paraffin eases driving.
- Although red oak sands readily, try garnet paper for hand-sanding and with orbital sanders. For belt sanders, we prefer oxide-type abrasives. Swirls and other sanding marks come off nearly effortlessly.
- For the smoothest possible finish, fill red oak’s grain with a paste-type filler. The filled wood (see photo, top right) has less dramatic grain contrast, but it requires fewer coats to build the final finish. For a lighter fill, sand surfaces with Danish oil as a lubricant. The sanded-off fiber packs the grain.
Carving comments
Only the most accomplished carvers tackle hard red oak, and then mostly for relief work. You won’t get far without a mallet and very sharp gouges. Some tips:
- Change from a shallow bevel (of 15°-20°) to a deeper bevel of 25°-30°when you rough-in the outline of a relief design. Your gouges stay sharp longer. Then, when it’s time to do the details and complete the carving, grind to a shallow bevel again for shaving.
- Our advice: Avoid slices along straight grain with stop cuts.
Turning tips
- When turning between centers, combat splinters by entering the wood with a sharp tool, such as a clean-cutting skew, and taking shallow cuts, especially when first rounding the turning square.
- Our turning tip: Keep tools sharp to cut rather than abrade. And, don’t start at one end and cut all the way to the other. Remove wood a little at a time in each section because the grain may run on a bias and splinter away.
SHOP-TESTED TECHNIQUES THAT ALWAYS WORK
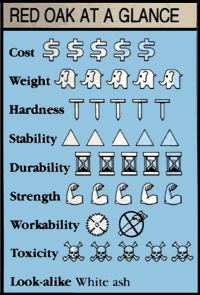
Any exceptions, and special tips pertaining to this issue’s featured wood species, appear under headings elsewhere on this page.
- For stability in use, always work wood with a maximum moisture content of 8 percent.
- Feed straight-grained wood into planer knives at a 90° angle. To avoid tearing, feed wood with figured or twisted grain at a slight angle (about 15°), and take shallow cuts of about 1/32″.
- For clean cuts, rip with a rip-profile blade that has 24-32 teeth. Smooth cross-cutting requires at least a 40-tooth blade.
- Avoid drilling with twist drills. They tend to wander and cause breakout. Use a backing board under the workpiece.
- Drill pilot holes for screws.
- Rout with sharp, preferably carbide-tipped, bits and take shallow passes to avoid burning.
- Carving hardwoods generally means shallow gouge bevels—15° to 20°—and shallow cuts.